people
On this page you can read about our vision and approach to how we work with our employees, the people in the value chain and our customers. At HEMA, we are there for everyone. We look after the people who work for us: in the Netherlands and the rest of Europe. And globally too: at our foreign purchasing offices and in the factories. In supplier factories, we work together to empower employees.
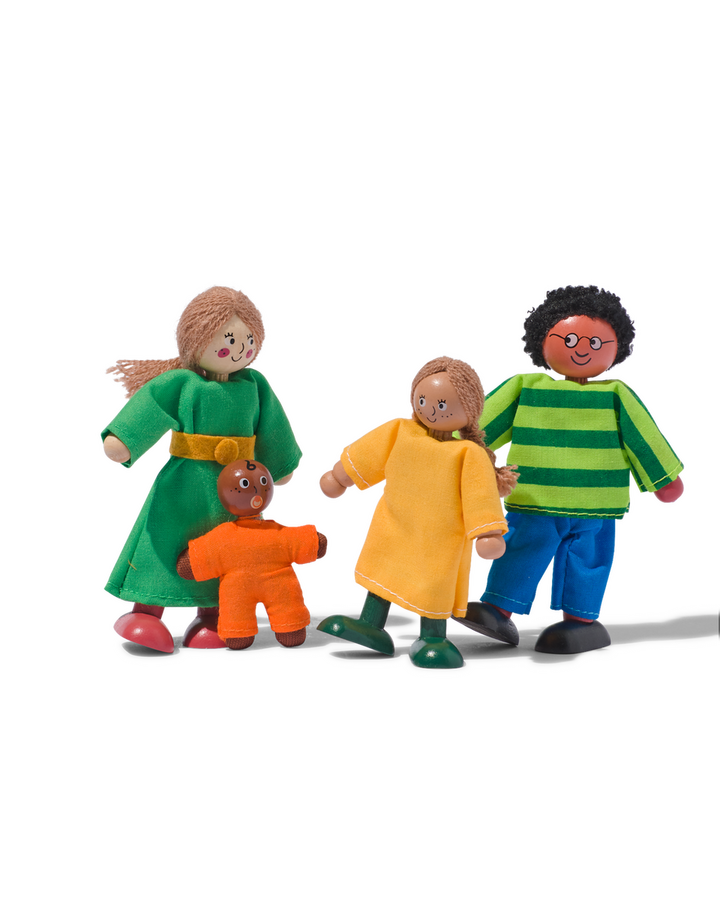
With this FSC® 100% certified wooden toy, you are contributing to responsible forest management worldwide. By choosing this product, you are helping to preserve forests and a more beautiful world.
scroll down
employees in shops, distribution centres and offices
We are proud of our 17,000 employees who are making HEMA truly HEMA again. Because of who they are and what they do. A little better every day. In the shops, distribution centres and offices in all our HEMA countries. Through four themes - be yourself, be brave, keep it simple and grow with us - we make sure our employees want to and continue working for HEMA and make HEMA truly HEMA again.
our employees in terms of figures 2023
HEMA had 9,889 employees (based on head count) on 31 January, 2024. In HEMA Netherlands, 99.99% of employees were covered by a collective labour agreement, this is unknown for other countries.
number of employees by gender
total | women | men | filled in otherwise | unknown |
---|---|---|---|---|
number of employees | ||||
9889 | 8128 | 1759 | 2 | |
number of permanent employees | ||||
5427 | 4290 | 1137 | 0 | |
number of temporary employees | ||||
4462 | 3864 | 596 | 2 | |
number of employees with contracts without a guaranteed number of hours | ||||
0 | 0 | 0 | 0 | |
number of full-time employees | ||||
2172 | 1088 | 860 | 0 | |
number of part-time employees | ||||
7717 | 6280 | 807 | 2 |
number of employees by region
The Netherlands | Belgium & Luxembourg | Austria | France | Germany | purchasing offices |
---|---|---|---|---|---|
number of employees | |||||
8118 | 852 | 76 | 549 | 234 | 60 |
number of permanent employees | |||||
3852 | 804 | 76 | 533 | 104 | 58 |
number of temporary employees | |||||
4266 | 48 | 0 | 16 | 130 | 2 |
number of employees with contracts without a guaranteed number of hours | |||||
0 | 0 | 0 | 0 | 0 | 0 |
number of full-time employees | |||||
1418 | 224 | 9 | 424 | 39 | 58 |
number of part-time employees | |||||
6700 | 628 | 67 | 125 | 195 | 2 |
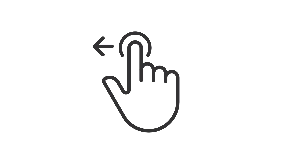
number of employees by age
total | % women | % men | % filled in otherwise | % unknown |
---|---|---|---|---|
<30 years old | ||||
4681 | 3982 84% | 697 16% | 2 <0,1% | 0 |
30-50 years | ||||
2833 | 2197 77% | 636 20% | 0 | 0 |
>50 years | ||||
2375 | 1951 82% | 424 18% | 0 | 0 |
employment conditions
We make virtually no distinction in employment conditions between full-time employees, except that employment conditions are allocated on a pro rata basis. In this, we have two exceptions: that employees working 12 hours or less can have their extra hours paid directly, and that the additional generation scheme only applies to employees working 20 hours or more. Additional hours do not apply to office-based employees, nor to salary scales 1-7.
training and development
Shops: vocational programmes, team leader programme, online training on shop processes, skills and personal development (e-learnings), vitality initiatives (workshops, challenges, vitality test), HEMA-100 training (for shops with the new shop concept by operations team (a.o. on customer focus, change management, product knowledge).
DC: vitality initiatives, leadership training by NONONS, MONDO behavioural workshops.
Office: onboarding programme and (online and physical), Summer Parade workshops (training day for all), leadership training MT+1 by QiQ, Good Habitz e-learnings, individual learning budget per employee of €70.
estimated hours (+/- 1770 hours) of training given to shop employees in the Netherlands.
Security | Knowledge sessions | 220 hours |
---|---|---|
SCO - theft and prevention from HEMA100 | 20 hours | |
Potential calls/online training SCO | 28 hours | |
Train the trainer sessions (regional trainers) | 26 hours | |
Improvement Action Plan explanation teams and online | 55 hours | |
(preparation adaptive training sco/customer experience) | 22 hours | |
Shop logistics | Basics in order: inventory management; region, TL days, knowledge sessions, other HEMA100 training courses | 1200 hours |
Safety | Knowledge sessions | 220 hours |
RI&E tool call introduction/explanation | 1 hour |
performance and career development appraisals
The majority of our employees have had at least 1 appraisal per year. This percentage is lower in France and Germany, because for example there is no HR manager in Germany.
performance and career development appraisal by gender
total | woman | man | other | |
---|---|---|---|---|
% of number of employees who had at least 1 appraisal per year. | 65,5% | 80,3% | 19,7% | 1 |
performance and career development appraisal by job role
total | job role | location | |
---|---|---|---|
% of number of employees who had at least 1 appraisal per year. | 5314 | Junior: 4789 Medior: 466 Senior: 59 | Office: 515 DC: 649 Shop: 4150 |
employees in the production chain
HEMA works with suppliers to make products. Together we keep making our products more sustainable and better. Our suppliers are all over the world. Some places pose a higher risk of violating human rights. We continuously monitor working conditions and work with suppliers and factories to bring about improvements.
We have developed a concrete policy and as such, closely monitor our production sites. In doing so, we are building transparency, policies and agreements. We set priorities in response to our risk analysis on human rights and environmental impact.
transparency
We are transparent about the factories that manufacture HEMA products and in which countries they are located. For example, external stakeholders are able to report any malpractice in an accessible way if they can directly see which factories produce for HEMA. Our suppliers and the factories that produce for HEMA have been publicly available on our website and the Open Supply Hub since 2019. In 2023, we added the food product category, which means that all factories, for all our product groups, are now public
due diligence
We follow the OECD Human Rights and Environmental Due Diligence guidelines. These are guidelines for companies to take chain responsibility and prevent, stop, or mitigate any negative impact. In 2023, we published our due diligence statement based on these guidelines. In it, we share what risks we have identified in the countries where HEMA products are made. Due to our diverse product range and chains, we base our approach on the highest (potential) risks. The output from our due diligence approach forms the basis for this prioritisation.
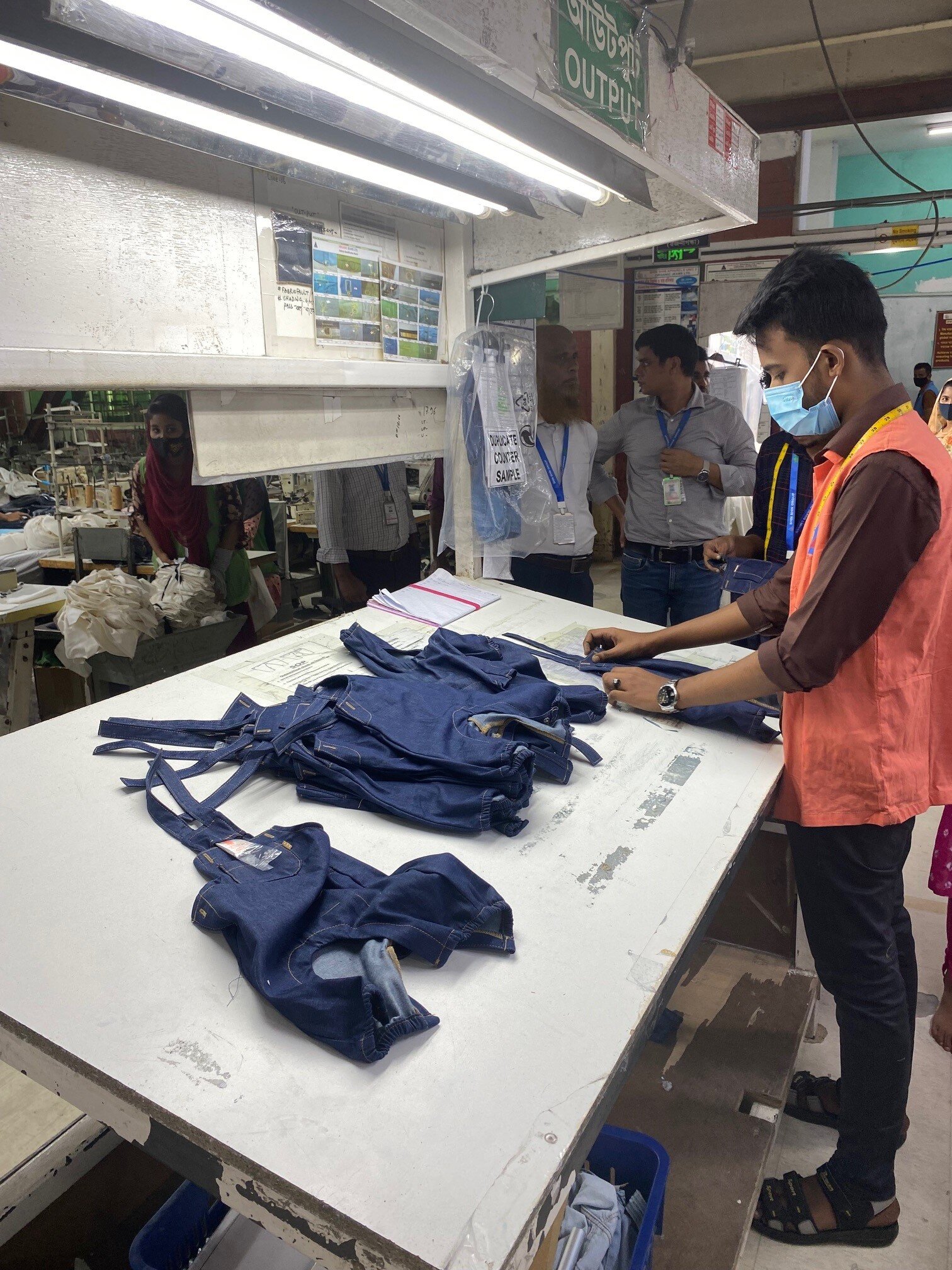
“2023 was all about dialogue. At our supply chain meeting in summer 2023, we discussed threats and opportunities, and how to improve our supply chain. We discussed ethical purchasing, along with how to empower employees in the supply chain. We gained valuable feedback, with the work being done by purchasing departments and working towards a fair wage being key priorities. In 2024 we will set about taking action in these areas."
Wilma Veldman
Chief Product Officer at HEMA
highlighted elements of our due diligence policy
working together for responsible purchasing
We have been part of the Learning and Implementation Community for Responsible Purchasing Practices (LIC) since 2022. Over the past few years, we have been working on implementing the five principles of the Common Framework on Responsible Purchasing Practices. For instance, we established new basic principles with an internal working group led by our Chief Product Officer (CPO) and colleagues from various departments.
working together for responsible purchasing
We have been part of the Learning and Implementation Community for Responsible Purchasing Practices (LIC) since 2022. Over the past few years, we have been working on implementing the five principles of the Common Framework on Responsible Purchasing Practices. For instance, we established new basic principles with an internal working group led by our Chief Product Officer (CPO) and colleagues from various departments. We have articulated those guiding principles in a new Supplier Code of Conduct. In 2024 we will define KPIs and provide training to the relevant departments. Among other things, we have established internal roadmaps for improving payment terms, forecasting and balancing orders. To measure the impact of our policies and actions, we will distribute a questionnaire to our suppliers, using a Supplier survey on responsible purchasing.
Supplier Code of Conduct
Our Code of Conduct is the basis for all collaborations with suppliers. At the beginning of 2024 HEMA drew up a new Code of Conduct: The HEMA Supplier Code of Conduct. Previously, the Code of Conduct described supplier responsibilities. We have now also added HEMA's responsibilities.
Supplier Code of Conduct
Our Code of Conduct is the basis for all collaborations with suppliers. At the beginning of 2024 HEMA drew up a new Code of Conduct: The HEMA Supplier Code of Conduct. Previously, the Code of Conduct described supplier responsibilities. We have now also added HEMA's responsibilities. The purpose of this is to strengthen collaborations based on equality and mutual respect, so that we know what to expect from each other.
Child labour policy
This describes the steps HEMA and the supplier take should child labour be suspected in the supply chain. In our policy and through monitoring, we seek to prevent child labour. In the unlikely event that it does occur, both HEMA and the supplier have a responsibility towards the child and its safety.
Child labour policy
This describes the steps HEMA and the supplier take should child labour be suspected in the supply chain. In our policy and through monitoring, we seek to prevent child labour. In the unlikely event that it does occur, both HEMA and the supplier have a responsibility towards the child and its safety.
HEMA exit strategy
This describes how HEMA can responsibly terminate a partnership with a factory. Paramount is the protection of workers in the factories and the potential impact a HEMA departure would have on them.
HEMA exit strategy
This describes how HEMA can responsibly terminate a partnership with a factory. Paramount is the protection of workers in the factories and the potential impact a HEMA departure would have on them.
grievance mechanisms
Effective grievance mechanisms, in and outside the factories, is one of the spearheads of HEMA's policy to empower employees. We have been working on this through various projects since 2019.
grievance mechanisms
Effective grievance mechanisms, in and outside the factories, is one of the spearheads of HEMA's policy to empower employees. We have been working on this through various projects since 2019.
By 2023, we further expanded our network to strengthen grievance mechanisms in our chains:
- As a member of Amfori, we joined the Speak for change programme. This programme is now active in Vietnam, India, Bangladesh, Turkey and Cambodia, among others.
- We have signed the Pakistan Accord.
- We re-signed the International Accord and the Bangladesh Agreement.
Our ambition is to have an effective external and independent grievance mechanism in our top five high-risk countries by 2025.
In 2023, a report of suspected child labour at a (illegal) sub-supplier was received through our purchasing office.
The actions we took are as follows:
- A warning to the supplier and factory.
- In consultation, agreed on better capacity planning.
- Conducted an unannounced visit to the sub-supplier, which did not find any violation of our Code of Conduct regarding child labour.
- At HEMA's request, UNICEF proposed improvements to our Child labour policy.
- We published the updated child labour policy.
- Policies around sub-suppliers are specifically stated in our new Supplier Code of Conduct, which includes HEMA's responsibility to coordinate capacity and production planning in consultation with the supplier.
- Capacity is something that is always assessed in the initial HEMA MRQ audit, which applies to all factories supplying HEMA.
A grievance mechanism is essential for identifying risks at production sites. In 2023, we received a total of 22 complaints through various channels. Below we describe the issues and how HEMA has been involved in redress.
Channel | No. of complaints | status | Subject | HEMA's commitment to redress |
---|---|---|---|---|
direct | 2 | 2 resolved | illegal use of sub-suppliers | Factory visit by purchasing office colleagues, unannounced visit to sub-supplier, improve capacity planning, 1 factory signed up for Amplify training. |
amfori | 1 | 1 in progress | Suspected forced labour | Written statement against forced labour. In progress, monitoring not yet completed. |
int. accord | 19 | 9 resolved 10 in progress | 13 entitled to severance pay; 4 intimidation; 2 other. | Direct communication with factory management from procurement office in Bangladesh. Other: resolved through Accord procedure. |
total | 22 | 11 resolved 11 in progress |
Number of complaints received in 2023, and how HEMA addressed them.
Concerns come to us through our grievance mechanism. On one occasion, we deployed our emergency response procedure. In November 2023, a fire occurred at a supplier to a factory producing for HEMA in Jiangsu province in China. The local government was directly involved. Together with the supplier, we inquired about developments and care for those directly affected. We spoke to and engaged other stakeholders. These incidents are also shared with our governance. Read more about our assurance of due diligence at more about our governance.
workers’ voice: Amplify
Since 2022, HEMA has been part of Amplify: a project where trade union freedom at production sites is central. Together with FNV and a local partner, we offered training to three factories in Bangladesh. The aim is to improve the collaboration between factory management and workers, and set up an independently elected workers' representation and train them to tackle improvements together.
workers’ voice: Amplify
Since 2022, HEMA has been part of Amplify: a project where trade union freedom at production sites is central. Together with FNV and a local partner, we offered training to three factories in Bangladesh. The aim is to improve the collaboration between factory management and workers, and set up an independently elected workers' representation and train them to tackle improvements together.
At the end of the training, we asked management and workers' representatives who had participated in the training a number of questions about the effectiveness of it. The results from the first factory are positive. When asked how the workers rated the training, eight out of 13 answered excellent. Five workers rated the training as excellent or good. The objectives were clear which helped them in their role as part of the employee committee. But one worker has not yet put the training into practice. The other 12 have used the training at least once for the benefit of the other workers in the factory.
Two management members completed the questionnaire. They rated the training as good and excellent. Both have used the training more than three times in liaison with the worker representative body. They perceived that the training improved communication between management and the worker representative body.
We will continue the training courses in 2024. Together with FNV, we are looking at a long-term project with the aim that all factories in Bangladesh have an independently elected worker representative body, effective dialogue and grievance mechanism.
living wage
Living wages are an important prerequisite for empowering workers in the production chain. It increases opportunities for children to go to school, buy healthy food or provide a solid and safe roof over their heads. This was reaffirmed at the chain meeting.
living wage
Living wages are an important prerequisite for empowering workers in the production chain. It increases opportunities for children to go to school, buy healthy food or provide a solid and safe roof over their heads. This was reaffirmed at the chain meeting.
HEMA is committed to this in three ways:
- By aligning with parties that advocate and work internationally to improve wages.
- By working with partners such as Amfori, IDH and others and reporting on wages.
- By working with our suppliers on ways to improve factory wages.
continuous improvement
Factories that will be making HEMA products are pre-audited by an external party on quality. This includes looking at capacity and potential use of sub-suppliers. Monitoring capacity is important to prevent illegal use of sub-suppliers. Factories in high-risk countries (according to the Amfori country classification) are also audited for social impact as well as quality. Our audit policy focuses on continuous improvement. We refer to this as our development approach. Audits are an important part of analysing and monitoring risks in our supply chain.
2023
HEMA re-signed the Pakistan Accord & Bangladesh Accord.
customers
For nearly 100 years, HEMA has captured a place in the hearts of our customers. Everyone comes to HEMA. And they can: we have accessible and cosy shops where our customers like to do their shopping.
During 2023 we implemented and tested a number of improvements to our shop concept, such as new self-scanning checkouts. Our customers were very satisfied with these modifications, so we will continue to revamp more shops in 2024. Customers can also enjoy shopping with us online, we are continuously improving our website. So that customers can more easily find what they are looking for.
4.88
8.010
loyalty card holders
in 2023
900.000
customers served
8,3
average
customer rating
45
NPS*
customer rating
8,5
CSAT*
scale from 1 to 10
*NPS: Net Promotor Score
*CSAT: Customer Satisfaction Score